Crafting the Future of Metal Fabrication
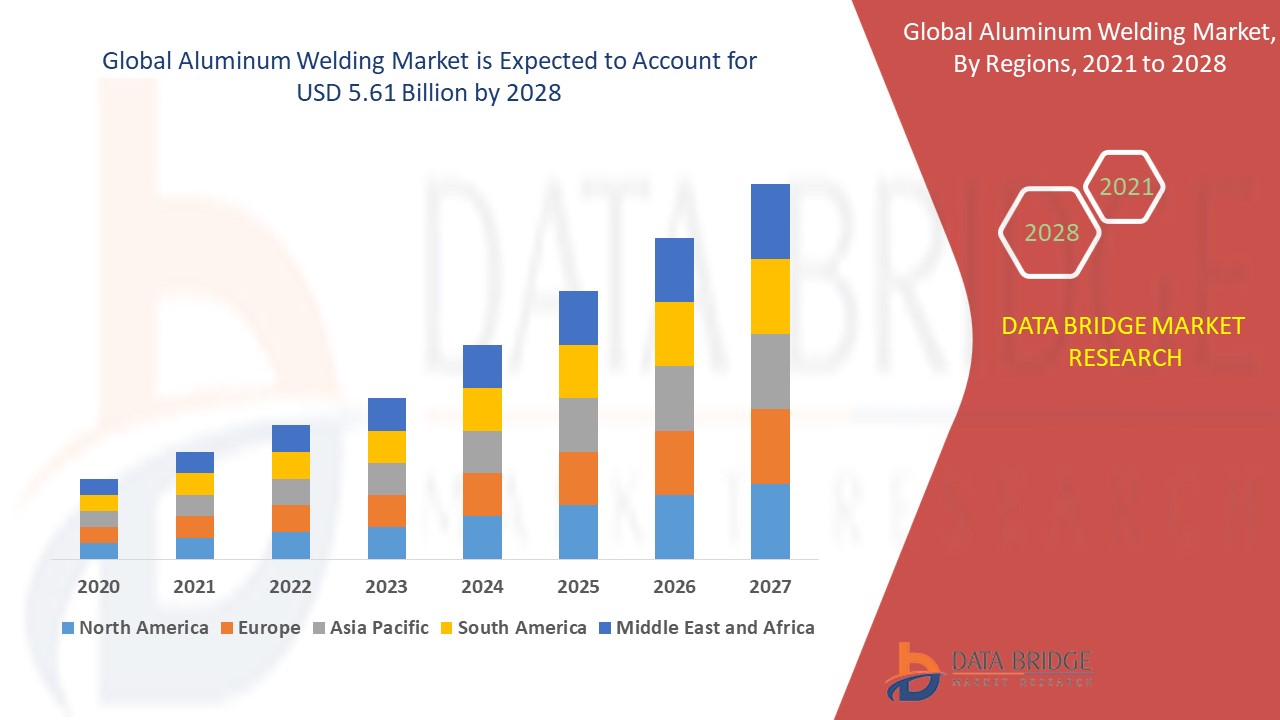
Introduction:
In the realm of metalworking, aluminum welding stands as a testament to precision and innovation. This process of joining aluminum alloys has evolved significantly, becoming a cornerstone of various industries, from automotive and aerospace to construction and manufacturing. Let’s embark on a journey through the world of aluminum welding, exploring its evolution, current market trends, and the factors driving its substantial growth.
The Evolution:
Aluminum welding has a rich history intertwined with the development of aluminum as a viable industrial material. Initially considered challenging to weld due to its unique properties, advancements in welding techniques and technology have propelled aluminum welding into a sophisticated process. The evolution of welding methods—from traditional techniques like gas metal arc welding (GMAW) to more advanced processes such as friction stir welding—has revolutionized the joining of aluminum alloys.
Over time, aluminum welding has evolved to meet the demands of modern industries. The quest for lighter and more durable materials in automotive and aerospace applications has driven innovation in aluminum welding processes. The development of specialized welding equipment, consumables, and shielding gases tailored for aluminum has further refined the welding process, ensuring high-quality and reliable welds.
Market Trends:
The market for aluminum welding has experienced a significant surge, mirroring the increasing demand for lightweight, high-strength materials across diverse sectors. In the automotive industry, aluminum’s use in vehicle construction has expanded, driven by stringent fuel efficiency standards and the pursuit of electric mobility. As automakers seek lighter alternatives to traditional steel, aluminum welding plays a crucial role in assembling vehicle components and frames.
Similarly, the aerospace sector has witnessed a growing reliance on aluminum alloys for aircraft manufacturing. Aluminum’s exceptional strength-to-weight ratio makes it an ideal choice for constructing aircraft structures, and welding techniques have been refined to ensure the integrity and reliability of joints in aerospace applications.
The construction industry has also embraced aluminum welding, leveraging its corrosion resistance and durability for structures, facades, and architectural elements. The adaptability of aluminum allows for intricate designs and innovative construction solutions, bolstering its use in both commercial and residential projects.
Factors Driving Growth:
Several factors contribute to the robust growth of aluminum welding in various industries. Technological advancements in welding equipment and techniques, such as the development of automated and robotic welding systems, have significantly enhanced productivity and precision in aluminum welding processes. These innovations reduce human error and increase efficiency, driving the adoption of aluminum welding across industries.
The lightweight nature of aluminum alloys remains a key driver for their widespread use and, consequently, the growth of aluminum welding. As industries prioritize fuel efficiency, reduced emissions, and improved performance, the demand for lightweight materials like aluminum continues to grow, boosting the need for reliable welding techniques to join these materials effectively.
Moreover, the emphasis on sustainability and recyclability aligns with the use of aluminum and its welding processes. Aluminum is highly recyclable, allowing for the efficient recovery and reuse of the material. Welding techniques designed for aluminum alloys support sustainability initiatives by facilitating the repair and recycling of aluminum components, reducing waste and environmental impact.
In conclusion, aluminum welding stands as a pivotal technique in the realm of metalworking, enabling the fabrication of lightweight, durable, and structurally sound products across multiple industries. Its evolution from a challenging material to weld to a versatile and indispensable part of modern manufacturing underscores the relentless pursuit of excellence in metal fabrication. As market trends emphasize lightweight materials, technological advancements, and sustainable practices, aluminum welding is poised to continue shaping the future of various industries, playing a pivotal role in crafting innovative and efficient solutions in the years ahead.
About Data Bridge Market Research:
An absolute way to predict what the future holds is to understand the current trend! Data Bridge Market Research presented itself as an unconventional and neoteric market research and consulting firm with an unparalleled level of resilience and integrated approaches. We are committed to uncovering the best market opportunities and nurturing effective information for your business to thrive in the marketplace. Data Bridge strives to provide appropriate solutions to complex business challenges and initiates an effortless decision-making process. Data Bridge is a set of pure wisdom and experience that was formulated and framed in 2015 in Pune.
Contact Us: –
Data Bridge Market Research
US: +1 888 387 2818
United Kingdom: +44 208 089 1725
Hong Kong: +852 8192 7475
Email: – [email protected]