Possible Details About Industrial reactors
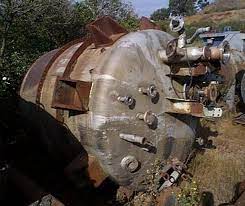
It is believed that the chemical reactors is the heart for any chemical process. It’s in charge of performing the process that converts ingredients into useful products. It’s typically one of the most expensive pieces of plant machinery.
Industrial reactors enable the creation of sustainably produced substances, such as fuels, chemicals and products. They can also reduce emissions of energy and waste.
Reactors for sale, Loaded
Reactors are machinery that is used to process chemicals so that chemical reactions occur. These types of reactions are commonly used to make products such as margarine and colorants. These reactions require special conditions to make sure that the reaction is speedily progressing towards the desired product. This means controlling the temperature, pressure, as well as the volume of the reactionants. Additionally, you must ensure that the reactants are thoroughly mixed.
The reactions can be carried out in batch or continuous systems. Batch reactors are sealed vessels that are filled with chemicals all at once. It allows the reactants to attain a stable state as a continuously operating reactor is able to be operated continuously and does not depend on the time it’s shut off.
Aaron Equipment offers a wide variety of new and used Industrial reactors for sale. These include glass lined and stainless steel reactor vessels manufactured by brands such as Pfaudler, De Dietrich, Brighton, and Roben. The reactors are rated for internal temperature and pressure as well as have ports for sensor input. They are also equipped with mixers for agitation and are designed to work with carbon or stainless steel jackets.
Reactors used in the past Amazing
Chemical reactions require extraordinary control for the process of turning reaction products into reactants. A device known as a reactor helps to achieve this. It consists of vessels that are able to hold the reactant mass, and also provide control of its properties like temperature, pressure and used reactors
. The vessel also shields employees from the dangers of toxic chemicals, as well as reduces the quantity of the energy as well as raw materials that are required to produce the desired product.
Reactors are offered in many shapes and sizes, ranging from small flasks or test tubes and the enormous structures seen in photos of industrial buildings. They’re generally made of strong, corrosion-resistant metals or glass. buy reactors also have nozzles and ports to add or removing substances, sources of radiation, either ultraviolet or heating as well as instruments that are specially designed to analyze pressure, temperature and other chemical properties.
There are two main types of Industrial reactors namely continuous and batch. used reactors are used for most processes that take place in a laboratory. Reactants are added to the reactor in small batches until they reach an appropriate conversion. They then cool and the products are discharged. Continuous reactors on side, run in a steady-state state. They are used in processes with heat transfer, mass transfer and catalysts.
Chemical Reactors Commonly Used
Chemical reactors chemical reactors is a container inside which controlled chemical reactions take place. The types of reactors can vary from small open kettles to the massive constructions seen in pictures of industrial plants. They are often made from materials that resist attack by the chemicals inside. Reactors may be utilized to carry out either the continuous or batch process. They are generally designed so that they can operate at high or low temperatures, as well as under pressure.
In a tubular reactor, liquids (gases as well as liquids) run through the process at a constant speed. This reduces back mixing the reactants as well as allowing they to transform into the products with a tremendous rate. This type of reactor is commonly used to perform hydrogenation and oxygenation reactions among other.
In certain chemical processes, it’s impossible to reach steady equilibrium (no net reaction). If this is the case, some sort of separation is required to segregate the reagents and byproducts from the desired end product. Feed contaminants can have significant impacts on the performance of an reactor and are very carefully chosen. Recycling reusable byproducts and by reducing feed contamination the process’s selectivity is enhanced.
Purchase reactors Circulated
In buy reactors used to produce poly(ethene) in which the catalyst and ethene are mixed with a diluting agent, typically the hydrocarbon and then distributed in a sequence of loops. The diluent evaporates, leaving the solid polymer which is collected at the foot at the bottom of one loop legs. The diluent is then cooled and the polymer is reformed as a liquid to be recirculated within the loop system.
The reaction takes place near the atmospheric pressure. This permits the creation of metal structures. This reduces price of costly, huge pressure-retaining equipment. Additionally, it allows operation over a wider temperature range than traditional CSTRs, and it eliminates the need for back-mixing.
Yet, many factors make it difficult for the US from engaging with other countries within the nuclear field. The most notable are deregulation of electric power market, the cost of natural gas, and financial incentives for renewable energies. These are the factors that have impeded efforts to produce and sell advanced nuclear technologies. In order to overcome these hurdles and to make progress, the DOE must encourage the next generation of tiny modular reactors (SMRs). This is the Natrium reactor is an excellent an example.
Industrial reactors types
Industrial reactors are employed for chemical reactions throughout a wide range of different industries. They are designed to contain the desired reaction and keep them under controlled conditions to ensure assurance and safety as well as efficiency. There are different types of Industrial reactors that include stirred tanks and tubular reactors. Every type of reactor has distinct properties and applications that make it a suitable choice for various industrial process.
In the case of a tubular reactor can have gas or liquid flowing through it at high velocities. These result in the reactants being converted to products with minimal back mixing. It is commonly referred to as plug flow, and it can drastically increase the amount of yield in reaction (Towler and Sinnott 2013,).